PROJECT STORY
#01
荷物を運ぶトラックボディを生み出す、
SGモータースのブレーン。
よりお客さまに寄り添った、開発・設計を実現するために。
-
営業部 開発課
開発チーム
吉竹 敦章 -
富士工場
設計チーム
佐藤 翔太 -
富士工場
設計チーム
北向 佑気
新車を製造する工程で、重要な存在であるのが開発・設計部門。年間1,500台以上もの働く自動車を生み出しているSGモータースにも、開発・設計部門がある。同社の開発・設計部門では、どのようにしてトラックボディを生み出しているのだろうか。
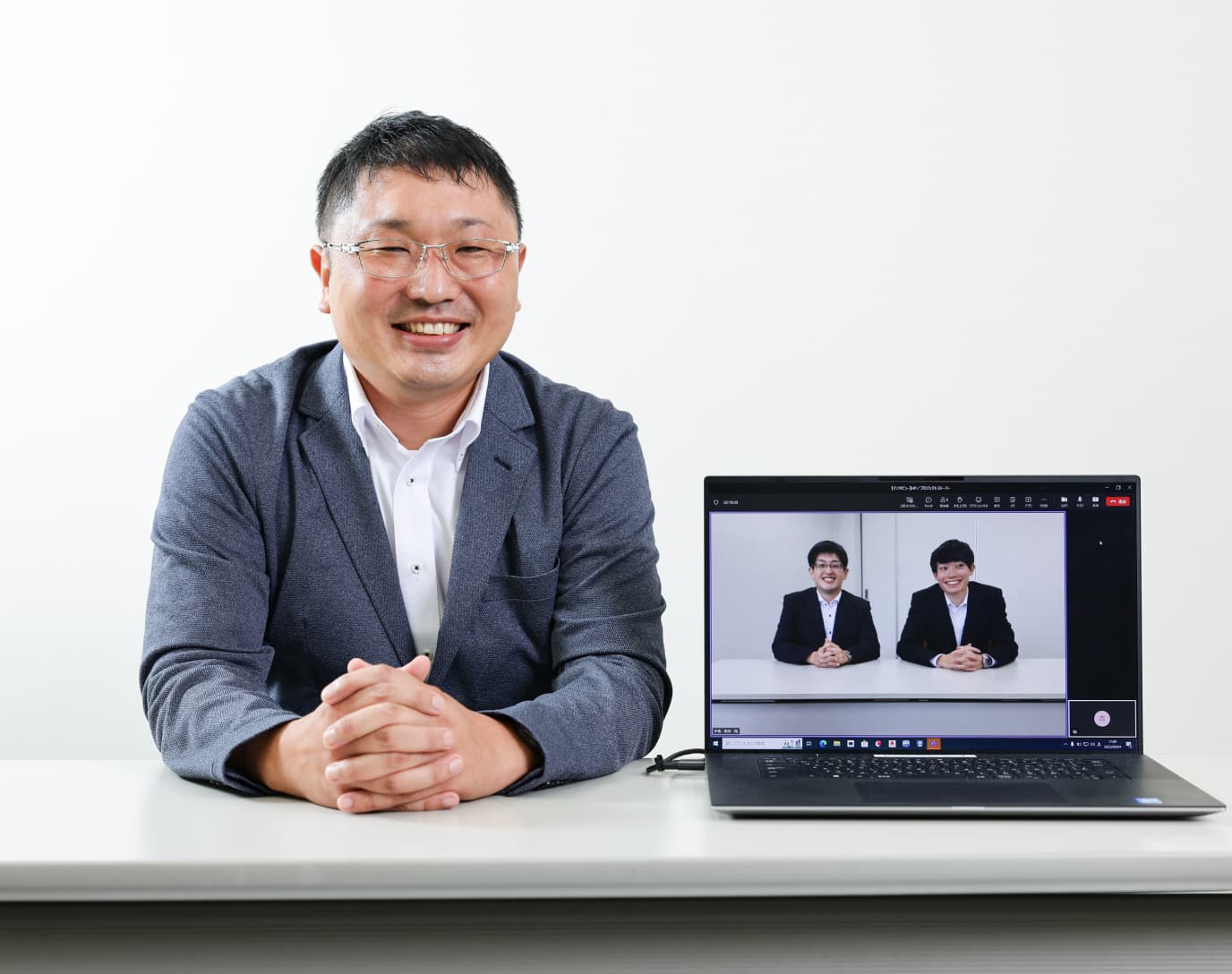
――前提となる設計・開発のプロセスとは。
SGモータースでは、主な車両として宅配便を運ぶ佐川急便のトラックボディ、そしてその他にも一般のお客さまからの車体の製造依頼も多数受けています。開発・設計部門では、そんな数多くのトラックボディや、それらに取り付ける部品の開発・設計を担っています。まずはお客さまや営業担当から、「こういったトラックが欲しい」「オプション部品を取り付けたい」といった、細かな指示が書かれた仕様書が入るところからスタートします。それらをもとに、『設計チーム』がトラックボディや取り付ける部品などの設計図を作成し、そこから、『開発チーム』がその設計図をもとに、試験機械などを用いて強度や安全性の評価・検証・解析を行いながら開発していきます。そうして仕様書からできあがったトラックボディや部品の「設計図」を製造工場に配布し、実際に製造・組み立てを進めていく、というのが一連の流れです。お客さまによって、日々さまざまな依頼が舞い込んでくるため、当然『設計チーム』から『開発チーム』への一辺倒な業務ではなく、密にやり取りを重ねながら、ニーズに沿ったカスタマイズを行っていきます。
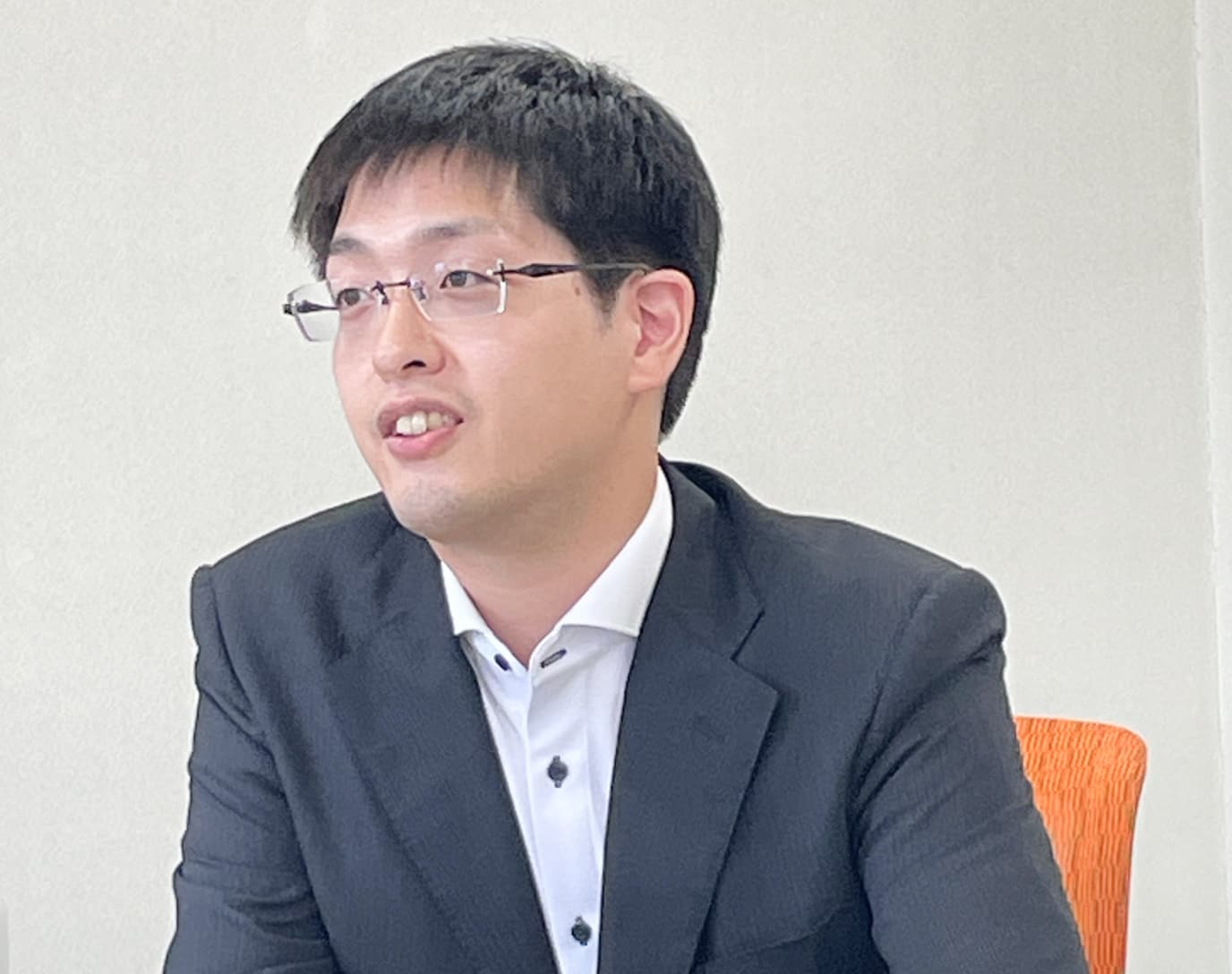
――試行錯誤する地道な工程が、新たな発想を生むことも。
設計の大切なポイント。それは、“経験”と“根気”そして“行動力”だと考えています。お客さまから依頼された内容を可能な限り車体や部品に反映するためには、過去の経験をもとに新しいデザインを考え、試行錯誤していくという地道な作業も多いからです。
例えば、“通常の倍近い大きさ・重さの冷蔵・冷凍庫を搭載したボディが欲しい”、“シャシの下部にオプションの架装品を邪魔にならないように取り付けてほしい”などの依頼が入ることがあります。そういった時、取り付けるためのスペースの計算から、設置による法規的な問題がないかの確認、さらには工場の架装工数・コストをいかに削減できるかといったところまで考慮しながら、構想を組み立てていかなければなりません。
簡単な仕事ではありませんが、こういった試行錯誤により、新たな着眼点から生み出すことができたデザインが採用された時は、達成感があり、そこがやりがいであったりするのです。
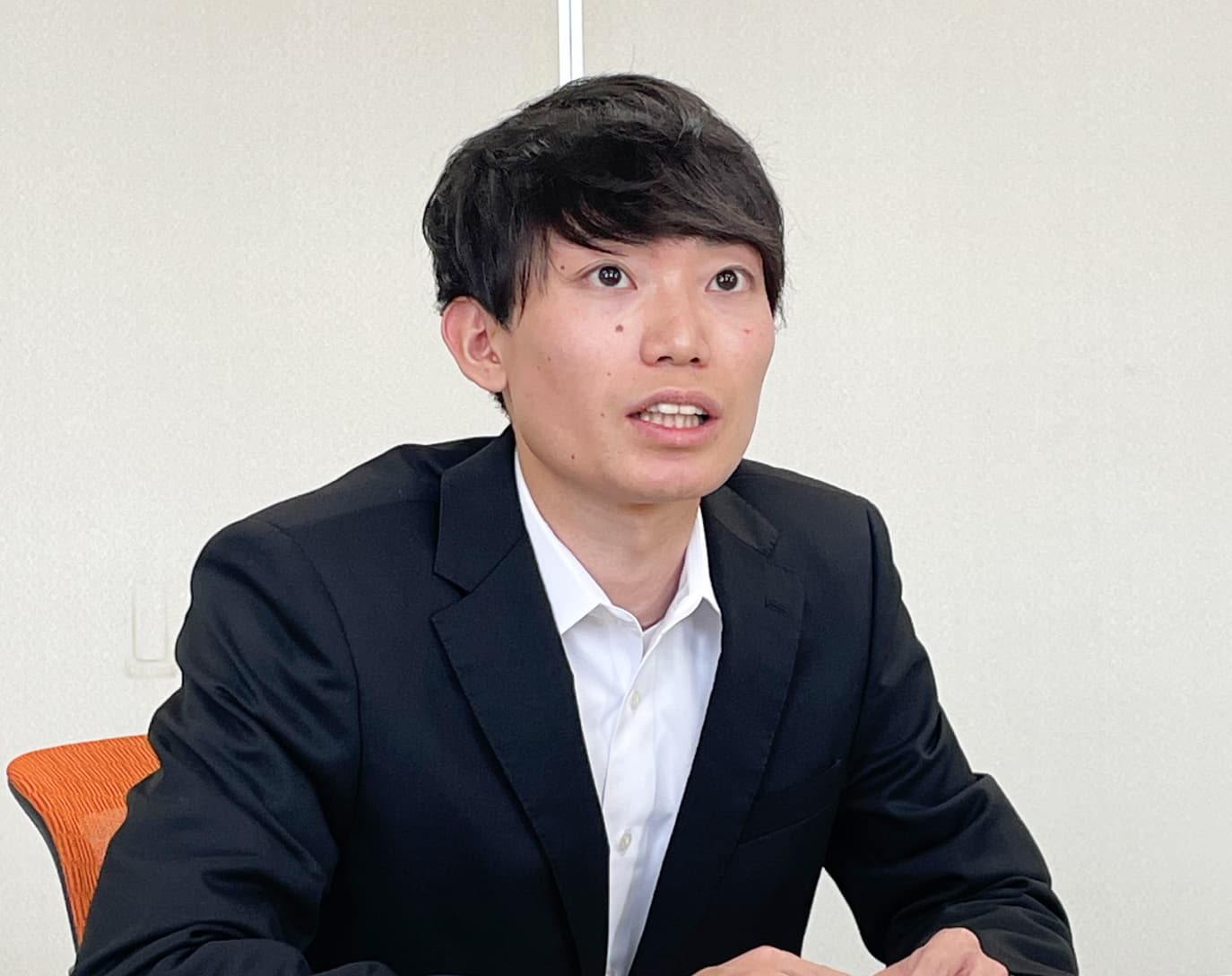
――あらゆる状況を想定し、安全性を追求した開発。
一方で、開発の大切なポイントは、+α“想像力”も重要なのです。例えば、“本来の部品の使い方に対して、実際のお客さまは全く別の使い方をするかもしれない”、“こんな状況で作業をしたら、怪我をするかもしれない”など、起こりうるあらゆる危険やリスクを想定しながら、開発をしていかなければならないからです。
開発チームは特に、評価・検証・解析を行いながら構造を確立させていく部門です。車体の腐食、耐久、耐震、耐温、あらゆる状況を想定し、検証を繰り返し、あるいは3Dプリンターを用いて、さまざまな素材で部品のサンプリングを試作し最も適したものは何かを検証していきます。
ときには、新しいボディ構造の架装を行う場合、同乗調査として、実際に助手席にのせていただき、どんな一日で、一日に扉を何回開けるのか、扉が開く幅はどれくらいなのか、荷台での作業状況や昇降時の体勢などの調査を1カ月近く行う場合もあります。お客さまへ、満足いただける商品をお届けするためには、あらゆる想定を仮定する想像力も重要です。
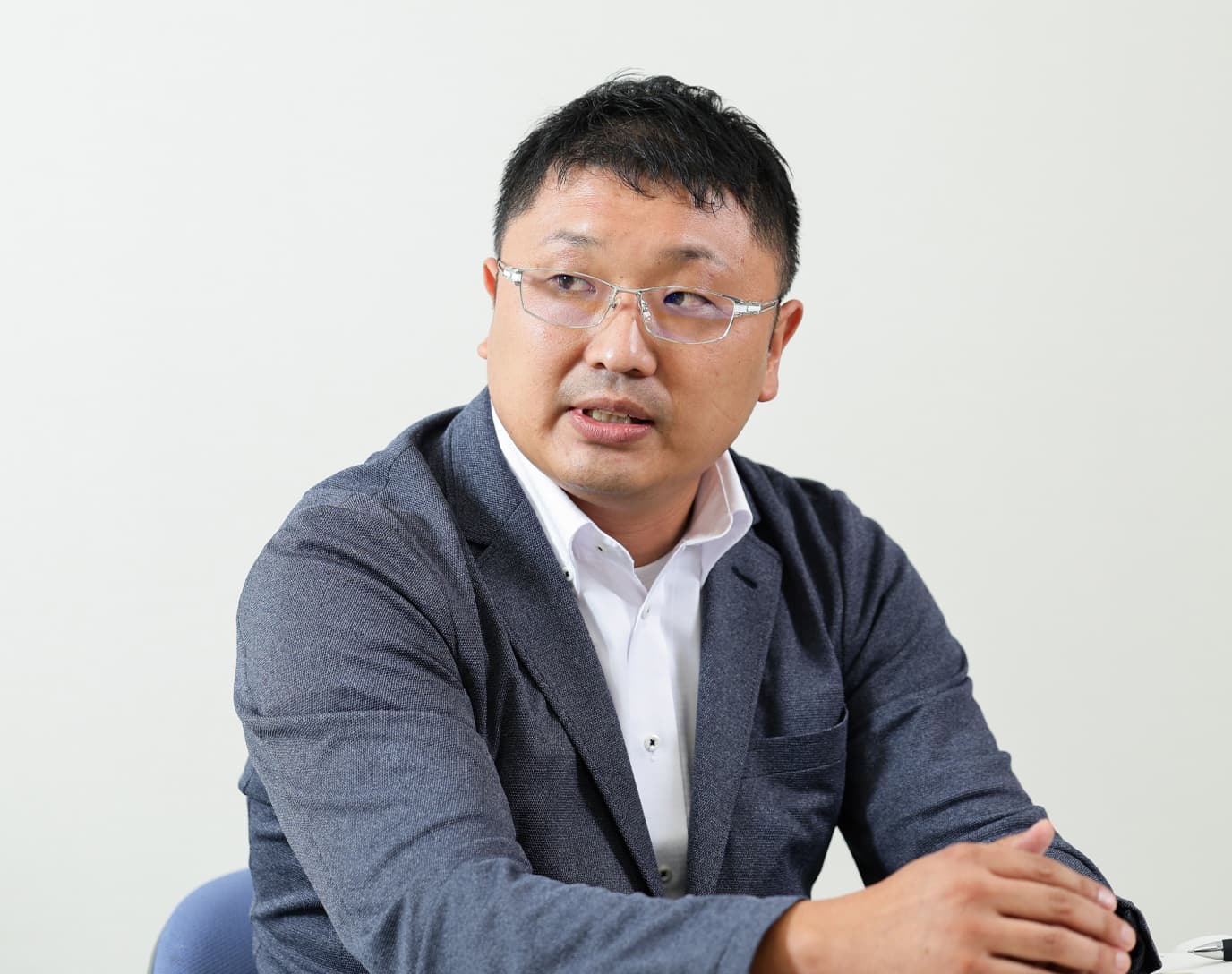
――日本の物流の未来を担い、サステナブルな社会実現にも貢献。
当社の開発チーム・設計チームの今後の展開としては、環境問題やSDGsに伴う新車両の開発です。トラックの電気自動車化が急速に進んでいる中で、部品の素材を一新する必要があり、今までにない方法や別視点から適切な方法で、それらの素材を目利きするために視野を広げていく必要があるのです。
働くトラックのさまざまなボディの開発・設計経験のあるSGモータースだからこそ、あらゆる柔軟な対応が可能な経験値の高いメンバーが数多く活躍しています。私たちは、それら独自の強みを活かし、日本の物流の未来を背負っていきたいと考えています。